Navigating the intricate world of industrial manufacturing, titanium oxide factories stand as pivotal entities in the production of one of the most versatile and widely used compounds in various industries. Titanium dioxide, known scientifically as TiO2, is renowned for its exceptional properties, including high refractive index, non-toxic nature, and brilliance, making it a critical component in products ranging from cosmetics to paint.
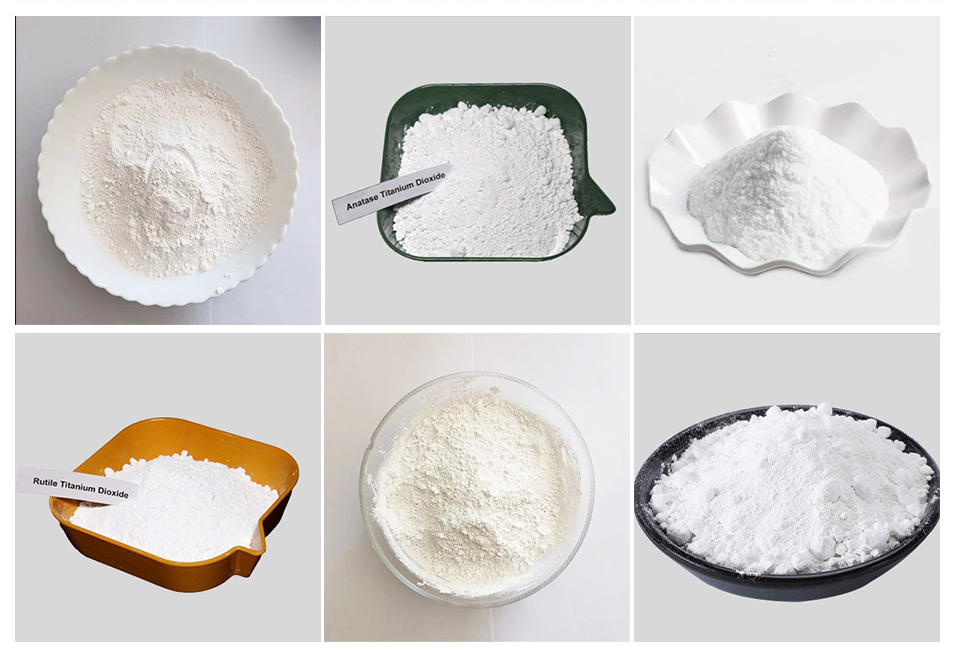
Firstly, understanding the core function of a titanium oxide factory is essential. These industrial powerhouses specialize in the extraction and processing of raw materials to yield titanium dioxide. The process typically begins with the mining of ilmenite and rutile, the primary ores from which titanium dioxide is derived. With expertise in both the sulfate and chloride processes, these factories convert raw minerals into pure TiO2, each method providing unique benefits in terms of purity and environmental impact.
The sulfate process involves digesting ilmenite with sulfuric acid, followed by precipitation and calcination, yielding titanium dioxide as an end product. This method is renowned for its ability to produce a variety of grades tailored to specific applications. On the other hand, the chloride process entails the chlorination of the ores to produce titanium tetrachloride, which is then oxidized to obtain pure titanium dioxide. This process is celebrated for its ability to produce a highly pure product with minimal waste.
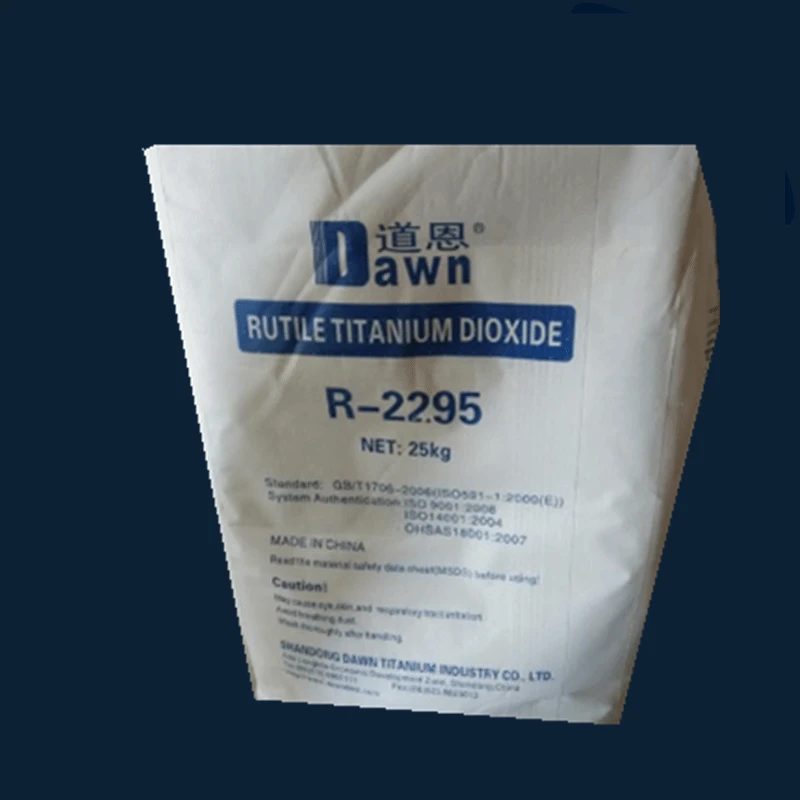
In terms of product expertise, titanium oxide factories excel in creating specialized TiO2 grades to meet diverse industry demands. For the paint industry, factories produce high-opacity titanium dioxide that enhances color brightness and durability. In cosmetics, TiO2 is valued for its UV filtering properties, making it a staple in sunscreen formulations. Additionally, these factories produce food-grade titanium dioxide, used as a whitening agent in various food products, adhering to stringent safety regulations to ensure consumer health and safety.
titanium oxide factory
The environmental and sustainability practices in titanium oxide manufacturing cannot be overstated. Factories are increasingly investing in state-of-the-art technologies and sustainable practices to minimize ecological impact. Through closed-loop recycling processes, waste products are reduced, and energy efficiency is maximized, aligning with global environmental standards and regulations.
Authoritativeness in the titanium oxide industry is demonstrated through continuous research and innovation. Leading factories invest significantly in R&D to develop cutting-edge TiO2 applications and advance existing technologies. By partnering with academic institutions and participating in industry-focused conferences, these factories contribute to the broader scientific community, ensuring the continued evolution and significance of titanium dioxide applications worldwide.
Trustworthiness in this sector is established through rigorous quality control measures and compliance with international standards such as ISO certifications. Each batch of titanium dioxide undergoes meticulous testing to verify its purity, particle size, and chemical composition, providing clients with reliable products that consistently meet their specifications. Furthermore, transparency about manufacturing processes and supply chain ethics strengthens trust with stakeholders, from raw material suppliers to end consumers.
In conclusion, titanium oxide factories are integral to the supply chain of a multitude of industries, underpinning their significance with a robust combination of experience, expertise, authoritativeness, and trustworthiness. Their commitment to refining production processes and enhancing product quality positions them as undisputed leaders in the global TiO2 market. As these factories continue to advance, they not only meet the ever-evolving demands of industry but also contribute to sustainable and ethical manufacturing practices, ensuring a brighter, more responsible future.