The intricate world of plastics manufacturing offers a spectrum of complexities, one of which is the incorporation of titanium dioxide. As an experienced player in the realm of factory production, understanding the multifaceted role of titanium dioxide in plastics is imperative for enhancing product quality and ensuring competitiveness in the market.
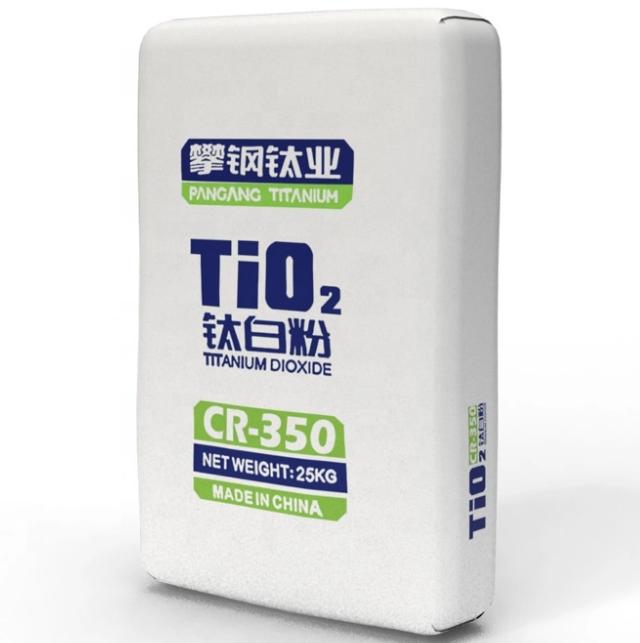
Titanium dioxide (TiO2) serves as an essential additive in the plastics industry, primarily revered for its ability to markedly enhance the whiteness and opacity of plastic products. Its utility in this domain blends a unique combination of chemistry and industrial application, making it indispensable for manufacturers focusing on aesthetics and functionality.
The core advantage of using titanium dioxide in plastics revolves around its exceptional light-scattering properties. As a pigment, TiO2 efficiently scatters visible light, which significantly improves the brightness and opacity of plastics. This characteristic is crucial for products requiring a pristine, uniform appearance, such as packaging materials, household goods, and automotive components. The enhanced opacity also provides better protection against UV radiation, which can degrade plastics over time.
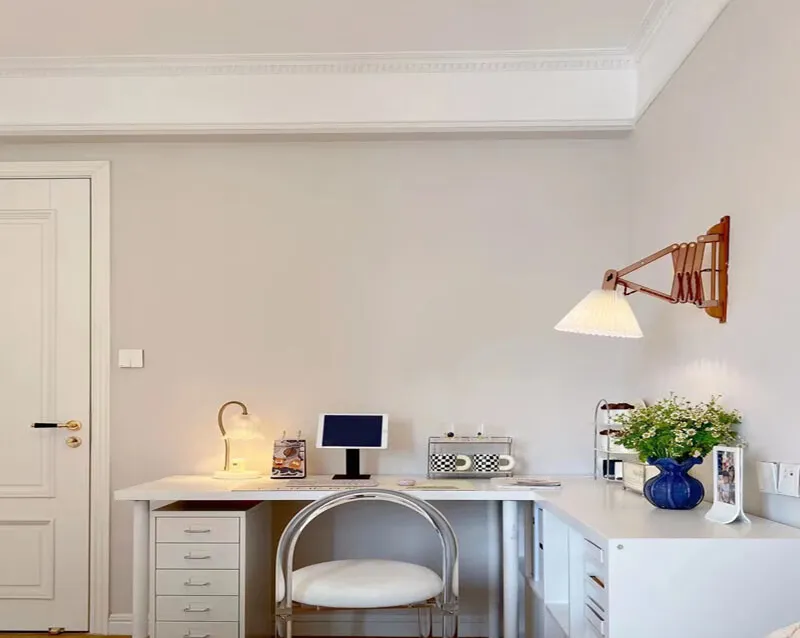
From an expert standpoint, the inclusion of titanium dioxide in plastics is not solely about visual appeal. For engineers and product developers, it's about achieving specific performance metrics that meet stringent regulatory and consumer standards. Titanium dioxide's effectiveness as a UV blocker extends the lifespan of plastic goods exposed to sunlight, thus preventing premature aging and preserving material integrity.
Authoritativeness in this field is drawn from an impeccable understanding of the technical nuances associated with titanium dioxide's interaction with polymers. Factory managers and production engineers must consider the dispersion quality of TiO2 within the plastic matrix to avoid agglomeration. Optimal dispersion not only ensures consistent color and opacity but also maintains the mechanical properties of the final product.
titanium dioxide in plastics factory
For plastics manufacturers, establishing trustworthiness involves adhering to robust quality control measures and environmental standards. There is a growing demand for product transparency and sustainable practices within this industry. Adopting titanium dioxide coatings, which often occupy a space in food packaging, must be conducted in accordance with health guidelines to prevent any potential migration of TiO2 particles that could pose health risks to consumers.
Efforts to sustain and improve the environmental footprint of titanium dioxide utilization have become increasingly significant. Modern factories are employing innovative techniques to recycle and filter off-cuts and emissions associated with TiO2 processing. Attention is also given to life cycle assessments that help in minimizing the ecological impact during the production, use, and disposal of titanium dioxide-infused plastics.
Furthermore,
titanium dioxide's application in plastics is continually evolving with advancements in nanotechnology. Cutting-edge developments are producing TiO2 nanoparticles which, due to their increased surface area, offer superior UV stabilization without altering the physical properties of the materials. This innovation presents a promising frontier for enhancing both the performance qualities and the ecological responsiveness of plastic products.
In conclusion, leveraging the full potential of titanium dioxide in plastic manufacturing demands a fine balance of experience and expertise. Being authoritative in this field means one must not only harness its properties for improved product performance and appeal but also navigate the complexities of health and environmental implications with unwavering diligence. As the industry progresses, maintaining a commitment to trustworthiness through sustainable practices and transparency will remain crucial for establishing long-lasting consumer confidence in titanium dioxide-enhanced plastic products.