Titanium dioxide (TiO2) equipment is paramount in the production and processing of TiO2, a pigment renowned for its brightness and high refractive index. Understanding the nuances of TiO2 equipment is essential for any enterprise aiming to optimize its production processes and reduce costs. This article explores the key aspects of TiO2 equipment, offering insights grounded in industry experience and expertise to foster trust and authoritativeness.
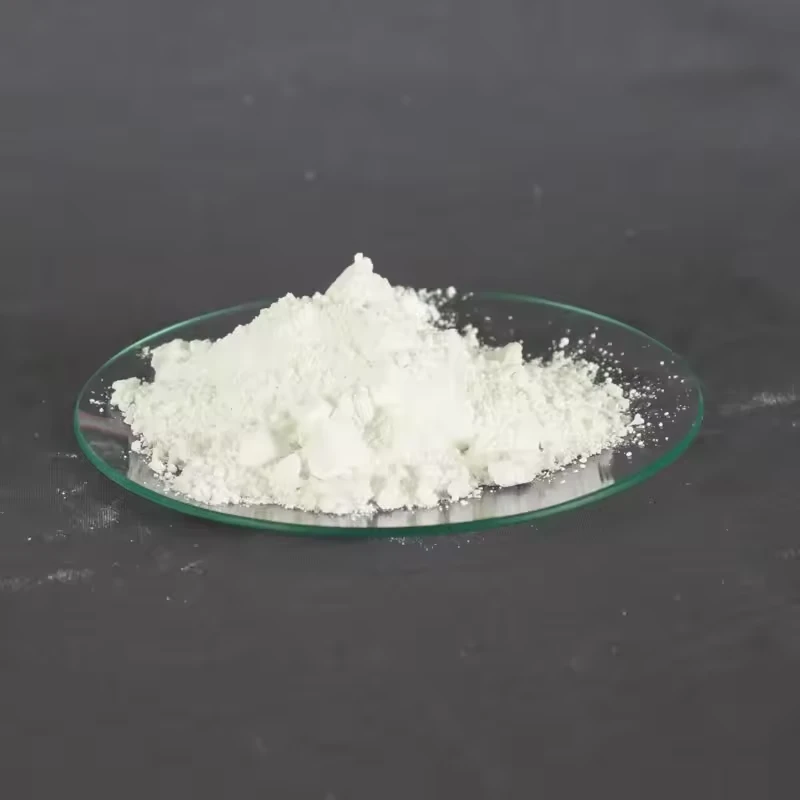
The selection of TiO2 equipment is critical in the context of the chemical and pigment manufacturing industry. The efficiency of the equipment directly influences the quality of the titanium dioxide produced. Equipment such as rotary kilns, grinding mills, and calciners are often employed. Each type of equipment comes with its specific operational parameters and maintenance requirements that influence overall productivity.
Rotary kilns are often used for the calcination of titanium dioxide, helping to remove any impurities and enhance the pigment's quality. Through years of industry use, it's become evident that regular maintenance of rotary kilns is essential to prevent downtime and ensure a consistent product quality. Adding experience-backed insights, operators might consider integrating a predictive maintenance schedule, replacing key components before failures occur based on historical data and usage patterns.
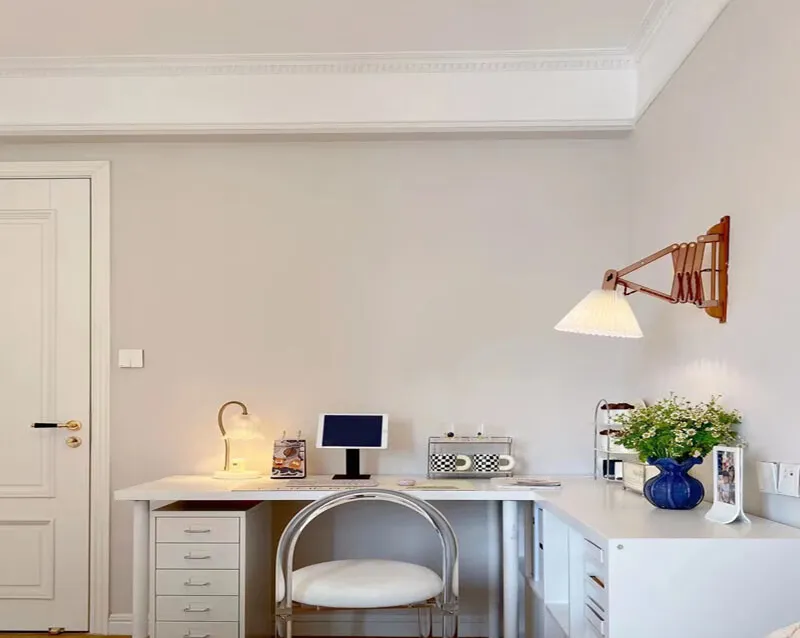
Grinding mills are tasked with achieving the right particle size distribution, crucial for the end product's performance in applications ranging from paints to sunscreen. Expertise suggests that a ball mill or a vertical roller mill be employed depending on the desired fineness and production capacity. Recent advancements have introduced automated roller mills that offer unrivaled efficiency and precision, leveraging AI to adjust components dynamically and enhance throughput.
Calciners, often used in conjunction with other TiO2 equipment, help in driving off volatile components and achieving the desired crystal structure. Expert opinion emphasizes the importance of uniform heat distribution within calciners, which can be achieved through advanced burner designs and computational fluid dynamics simulations that ensure even temperatures throughout the calcining chamber.
tio2 equipment
Beyond the individual components, the integration of TiO2 equipment into the broader production line must be carefully managed. Effective layout planning can minimize material handling costs and help streamline the entire process. Trustworthiness in system design can be showcased by adhering to industry standards and employing proven project management methodologies during the planning and installation of production lines.
From an operator's perspective, experience has shown that the human element is as crucial as the technology itself. Thorough training programs and an emphasis on safety can significantly reduce the risk of accidents and operational errors, thus maintaining high productivity and quality standards. An authoritative training program draws on industry best practices and utilizes up-to-date learning materials, simulations, and regular assessment quizzes to ensure that operators are well-versed in the latest techniques and safety protocols.
Quality control remains a pillar of TiO2 production, and trustworthiness can be bolstered by investing in state-of-the-art quality testing labs equipped to perform rigorous analysis. X-ray diffraction (XRD) and scanning electron microscopy (SEM) are indispensable tools that provide insights into crystalline structure and particle size, respectively. Implementing a quality control system that pairs cutting-edge technology with rigorous oversight from experienced personnel solidifies a company's reputation for high standards.
Sustainability is a growing concern in TiO2 production; thus, optimizing equipment for energy efficiency and waste reduction is crucial. Variable-frequency drives (VFDs) and other energy-saving technologies in mills and kilns reduce electrical consumption significantly. Waste treatment facilities specifically designed for handling by-products of TiO2 manufacturing can ensure compliance with environmental regulations and project an image of responsibility and commitment to the planet.
To conclude, selecting and maintaining the right TiO2 equipment involves a delicate balance of knowledge, experience, and strategic foresight. By appropriately leveraging advanced technology, adhering to best practices, and prioritizing sustainability, companies can excel in an industry that demands the utmost in quality and efficiency. Emphasizing these core principles will not only improve operational effectiveness but will also enhance the credibility and authority of the business within the competitive landscape of TiO2 manufacturing.